INTERNET OF THINGS
The future is already our reality!
Industry 4.0 is revolutionizing the way companies manufacture, improve and distribute their products. Manufacturers are integrating enabling technologies including the Internet of Things (IoT), cloud computing and analytics, as well as AI and machine learning into their production facilities and throughout their operations.
These smart factories are equipped with advanced sensors, integrated software and robotics that collect and analyze data and enable better decision-making.
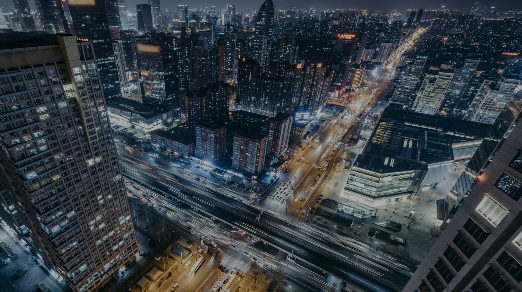
INTERNET OF THINGS
What technologies are driving Industry 4.0?
We are now in the fourth industrial revolution, also referred to as Industry 4.0, which is characterized by increasing automation and the use of smart factories informed by data to produce goods more efficiently and productively.
Flexibility is improved so that manufacturers can better meet customer demands using mass customization, ultimately seeking to achieve efficiency with, in many cases, a single small batch.
By collecting more data from the shop floor and combining it with the company's other operational data, a smart factory enables better decisions to be made.
Internet of ThingsThe Internet of Things (IoT) is a fundamental component of smart factories. Machines on the factory floor are equipped with sensors that include an IP address that allows the machines to connect with other web-enabled devices.
AI and Machine LearningAI and machine learning allow manufacturing companies to take full advantage of the volume of information generated not only on the shop floor, but across their business units and even from partners and third-party sources.
Cloud ComputingCloud computing is the basis of any Industry 4.0 strategy. The full implementation of smart manufacturing requires connectivity and integration of engineering, supply chain, production, sales and distribution, and service. The cloud helps make this possible.
Edge ComputingThe demands of real-time production operations mean that some data analysis must be done at the "edge", i.e. where the data is created. This minimizes the latency time from when the data is produced to when a response is required. For example, detecting a safety or quality problem may require near real-time action with the equipment.